Posted on Thu, 11/18/2021 - 20:58
By Mark Lowey, CESAR communications advisor
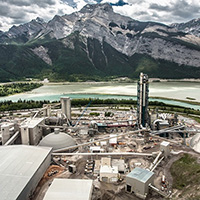
The world uses about 4.1 gigatonnes of cement each year, resulting in approximately 2.3 gigatonnes of carbon dioxide (CO2) emissions annually from the global cement industry.
If the cement industry were a country, it would generate more CO2 emissions than any other nation except China and the U.S. – about eight per cent of all anthropogenic CO2 emissions. Also, worldwide demand for cement is projected to grow.
“If we want to transition to net-zero emissions by 2050, then we need to decarbonize the cement sector,” says Daya Nhuchhen, an energy systems analyst at CESAR.
Nhuchhen, who is from Nepal, earned his PhD in Mechanical Engineering from Dalhousie University in Halifax, and has expertise in bioenergy, waste-to-energy, and sustainability. A professional engineer and a member of the Association of Professional Engineers and Geoscientists of Alberta, he also has certification, from KHD Humboldt Wedag, in cement production and burner operation.
Getting to net-zero emissions in the energy-intensive cement industry is not a simple matter, according to two CESAR studies led by Nhuchhen and co-authored by Song P. Sit, a senior associate at CESAR, and David B. Layzell, CESAR’s director and energy systems architect at The Transition Accelerator.
The first study, “Alternative fuels co-fired with natural gas in the pre-calciner of a cement plant: Energy and material flows,” looked at the thermal energy demand and other impacts of using alternative fuels in a natural gas-fired cement plant, including whether this could significantly reduce CO2 emissions.
Researchers framed their study on Lafarge-Holcim’s cement plant in Exshaw, the only gas-fired cement plant in Alberta. The company is exploring the potential to use alternative fuels at the plant to both reduce the fuel cost and the CO2 emissions intensity for clinker production. Clinker, the glassy product of fusing together clay and limestone, is used to make cement.
Nhuchhen and CESAR researchers developed a thermal energy flow (TEF) model for a cement plant with a capacity of 4,200 tonnes per day of clinker.
The TEF model was designed to assess the performance of a gas-fired cement plant in which 50 per cent of the pre-calciner energy requirements can be supplied by solid alternative fuels, including biomass and plastic waste. (The pre-calciner unit in a cement plant uniformly disperses and suspends the raw materials used to make cement in airflow, making fuel combustion and limestone decomposition faster).
Natural gas is a low-carbon fuel, with a carbon intensity of about 56 kilograms of CO2 per gigajoule, Nhuchhen notes. In comparison, cement plants fuel by coal or petroleum coke have a carbon intensity of about 90 to 95 kg of CO2 per gigajoule.
Alternative fuels can increase overall CO2 emissions intensity
The CESAR study looked at 24 waste-derived alternative fuels. Researchers developed a detailed TEF model for three of these fuels: high-density polythene or plastic waste, wood dust and railway ties. They analyzed how the embedded elemental oxygen content, lower heating value, and moisture content of the alternative fuels affected thermal energy intensity, air demand, and CO2 emissions intensity.
To ensure complete combustion in the cement-making process, their TEF model takes into account that solid alternative fuels must be supplied with more air (also known as “excess oxygen”) than that needed by a cement plant fueled only with natural gas.
Given these parameters, “the TEF model showed that the energy requirements for clinker production could go up by as much as 13 per cent if alternative fuels replace 50 per cent of the pre-calciner energy demand,” Nhuchhen says.
This additional energy demand is mostly required to heat the 20- to 21-per-cent increase in demand for air when alternative fuels are used, he notes. With increased air supply, electricity demand also rises to run fans and other equipment to manage the higher volume of gases, he adds.
The TEF model showed that using plastic waste (which has no biogenic carbon) as alternative fuel, to replace 50 per cent of the pre-calciner energy demand, would increase the overall carbon intensity of cement production by approximately six per cent. Fifty per cent of the pre-calciner energy demand amounts to 30 per cent of the total natural gas demand in a cement plant.
Researchers also ran their model to analyze the impacts of using wood dust, an alternative fuel that is 100-per cent biogenic carbon. Wood dust reduced the CO2 emissions from fuel combustion by about 43 kg of CO2 per tonne, despite the increase in fuel energy demand. However, this reduction is only about six per cent of total overall emissions.
“If we want to get to net-zero emissions or completely decarbonize the cement industry, switching to alternative fuels cannot get us there,” Nhuchhen says.
CESAR Director Layzell points out that more than half of the GHG emissions from a cement plant aren’t from fuel combustion, but from the CO2 that’s embedded in limestone and released when the limestone is heated in the pre-calciner and kiln.
“Such ‘process’ emissions are more challenging to mitigate than the energy emissions,” Layzell says.
Therefore, the CESAR study concluded that using alternative fuels can achieve an incremental reduction in GHG emissions if the alternative fuel is biomass-based. But if the alternative fuel, such as plastic waste, has a fossil-carbon source, the GHG emissions are likely to be higher than that for a cement plant fueled only by natural gas.
“Of course, alternative fuels are often diverted from landfill, so they can be lower cost than conventional fuels. This can provide another incentive for their use,” Nhuchhen says.
Assessment tool developed for cement plant operators
In addition to their thermal energy flow model, Nhuchhen and CESAR researchers also developed a “regression equation” as a simpler and quicker tool that cement plant operators can use to assess the costs, energy demand changes and other impacts of using alternative fuels.
Their equation is based on four key parameters that affect energy demand in a cement plant:
- moisture in the fuel;
- energy content in the fuel;
- elemental oxygen embedded in the fuel; and
- oxygen needed to fully combust the fuel.
The regression equation would enable cement plant operators to quickly determine the impacts of co-firing, with natural gas fuel, an alternative fuel containing 20-per-cent moisture, for example.
That may give operators some options, such as drying the alternative fuel before use or mixing it with other fuels that have higher energy value, Nhuchhen says.
Another consideration in using alternative fuels is the amount of fuel needed to co-fire with natural gas fuel in a cement plant.
For example, it would require some 56,000 tonnes per day of wood dust to meet 30 per cent of the fuel demand in a gas-fired cement plant, Nhuchhen says. “So unless an abundant amount is available, it may be difficult for operators to rely only on wood dust or another sole alternative fuel feedstock.”
“Partnerships are essential to our mandate to move toward a more circular and sustainable business model,” says Robert Cumming, head of sustainability & public affairs, Eastern Canada, at Lafarge Canada. “The CESAR research team’s work with us has informed our plans and has accelerated our drive to decarbonize our operations. We are delighted with the work and reports that came out of this partnership.”
Lafarge is currently co-firing alternative fuels, including wood dust, powder made from rubber tires, and plastic waste, in its natural gas-fired cement plant in Richmond, B.C.
The Richmond plant also includes carbon capture technology developed by Svante Inc., enabling Lafarge to capture the CO2 contained in the plant’s flue gas and reuse it for CO2-cured concrete, thus storing it permanently.
This CESAR study was supported by Alberta Innovates, Emissions Reduction Alberta, Natural Sciences and Engineering Research Council of Canada, and LafargeHolcium Inc.