Posted on Tue, 02/09/2016 - 07:39
By Mark Lowey
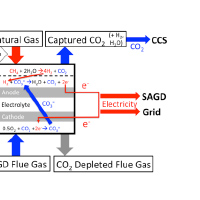
Figure 1. The students who carried out the MCFC-SAGD project described here did so in fall 2015 as part of a capstone project in the Scie529 course that is taught by CESAR Director David Layzell. Students Bright, Fritz and Subramanian are training to be chemical engineers while Robinson and Stegeman are training to be mechanical engineers.
Integrating the fuel cell technology into oil sands operations using steam assisted gravity drainage (SAGD) would reduce overall greenhouse gas emissions in Alberta by 25 million tonnes (Mt) CO2e per year by 2037, resulting in total reductions of 298 Mt CO2e between 2020 and 2040, their modelling projections found (Figure 2).
That includes emissions reduced at SAGD operations, as well as from ‘greening’ the province’s electrical grid. Clean electricity generated by the fuel cells that is surplus to the power required by SAGD facilities would be supplied to the grid, to offset more carbon-intensive electricity such as coal power. Alberta’s total greenhouse gas emissions in 2014 were 264 Mt CO2e.
Figure 2. The projected (2010 to 2060) greenhouse gas (GHG) emissions released from Alberta’s SAGD oil sands operations and from the electrical grid under a Business-As-Usual scenario (Panel A) and an Alternative scenario (Panel B). In the Alternative scenario, between 2020 and 2037, molten carbonate fuel cells are deployed to capture 50% of the CO2 produced in SAGD steam generation, and all surplus power is put on the electrical grid.
To achieve the emissions-reductions projected in the study, molten carbonate fuel cell (MCFC) technology would need to be deployed across 900,000 barrels per day of bitumen produced, or about half the total daily production from SAGD operations expected by 2037.
Implementing MCFCs in SAGD operations also would be potentially cost-effective under the provincial government’s planned $30-per-tonne carbon tax, the study showed.
“We’re optimistic that molten carbonate fuel cells have the potential to dramatically reduce greenhouse gas emissions from Alberta’s oil sands, while also directly reducing emissions from Alberta’s electrical grid,” says Jordan Robinson, a fourth-year mechanical engineering student and spokesman for the team.
“With proactive investment in MCFC development by government and industry and a streamlined regulatory approval process, MCFCs could potentially cut emissions by 25 million tonnes of CO2e each year by 2037,” Robinson says. “Our project raises awareness of the critical role of technology assessment research in moving towards a more sustainable energy future.”
A major challenge with SAGD operations is the large quantity of greenhouse gas (GHG) emissions released into the atmosphere when natural gas is burned to produce steam – thereby contributing to global warming and climate change.
High GHG emissions in Alberta’s oil sands are undermining public support for future projects and market access to export bitumen, via such proposals as the Energy East pipeline to Canada’s East Coast and the Trans Mountain pipeline expansion to the West Coast.
“There is a critical need for a transformative technology that can be incorporated into SAGD facilities to lower the GHG intensity of oil sands and compete economically with the province’s new carbon tax,” Layzell says.
In 2014, the 21 SAGD oil sands facilities currently operating in Alberta released a total of 24 Mt of CO2e – equivalent to a GHG emissions intensity of 76.3 kg of CO2e for every barrel of bitumen produced.
Figure 3. The average greenhouse gas (GHG) intensities associated with crude oil recovery (kg CO2e/bbl) from a range of crude oils produced around the world. Note that crude oil produced by the SAGD-MCFC Integration scenario in 2040 was projected to have a lower GHG intensity than that in the SAGD Business-As-Usual case.
Using molten carbonate fuel cells to remove CO2 from SAGD steam generation and store it safely underground in saline aquifers would provide both steam and electricity with much lower GHG emissions intensity. For SAGD operations, oil could be produced at about 35 kg of CO2e per barrel, equivalent to the GHG intensity of conventional oil (Figure 3).
Molten carbon fuel cells have been used in commercial power generation (megawatt-sized plants) since the 2000s, but have not yet been deployed at commercial scale to capture carbon dioxide. In 2015, the U.S. Department of Energy announced it would provide funding to Connecticut-based FuelCell Energy Inc. to develop a megawatt-scale molten carbonate fuel cell system that captures CO2 from coal-fired power generation. (Click here for more information).
Figure 4. In a molten carbonate fuel cell (MCFC) the CO2-containing flue gas from the SAGD steam generator is provided to the cathode and natural gas and steam are provided to the anode. At the anode, the CH4 and steam are converted to H2 (internal reforming) and the H2 reacts with carbonate ion (CO3=) that has diffused from the cathode. This results in the production of nearly pure CO2 (which can be compressed and sequestered) plus electrons that can generate an electrical current that provides power to meet the needs the SAGD operation and supply the electrical grid. (Modified from Jacobs Consultancy, 2015).
MCFC technology could be adapted to capture CO2 at commercial scale, says Song P. Sit, a retired chemical engineer who worked for many years in the oil sands industry and volunteered as one of two expert advisors for the CESAR-coordinated study. (See Figure 4 for an overview of how a MCFC operates).
Any deployment of MCFCs would likely start small, Sit said, with a one- to five-megawatt demonstration unit built and operating from 2016 to 2020, and then possibly a 50- to 100-MW commercial unit by 2030.
“The SAGD industry would do the demonstration unit to show good faith and that they’re serious about deploying the technology commercially,” he said.
However, for widespread deployment of MCFCs in SAGD facilities to be economically feasible, government incentives – beyond the province’s $30-per-tonne carbon tax to start 2018 – would be required, or the capital costs of MCFC technology would have to come down, Sit said.
The study also found that integrated molten carbonate fuel cell-SAGD technology could help in phasing out 1,336 megawatts of coal-fired power by 2037. Clean electricity generated by MCFCs would reduce GHG emissions from the grid to 25 Mt of CO2e per year by 2037, from the current 38 Mt per year.
“I think MCFC technology is very promising for steam generation and CO2 capture in the oil sands,” says Viola Birss, University of Calgary professor of chemistry, Canada Research Chair (Fuel Cells and Related Clean Energy Systems), and director of Calgary Advanced Energy Storage and Conversion Research Technologies. She advised on the CESAR study.
There are no insurmountable technical challenges in adapting MCFCs to capture CO2, she says, adding that potential issues – as with all fuel cell technologies – include durability of materials and operational longevity.
Birss says she is seeing a trend toward lower costs for other types of fuel cell technologies, such as PEM (proton exchange membrane) fuel cells. The costs of any technology tend to drop with economies of scale, as an expanding market reduces production costs, she says.
To carry out their work, the students started with CESAR’s Business-As-Usual Low Oil Sands Growth scenario for Alberta (described here in CESAR’s Jan. 26, 2016 blog). They then modified this scenario using detailed technical data from two recent studies1,2 that explored the techno-economics of integrating MCFC technologies into SAGD facilities.
“Scenario modeling like this can provide valuable insights to policy makers and those wanting to invest in promising technologies that can transform our energy systems towards sustainability,” Layzell noted.
The team produced a scientific poster as well as a report on the project detailing their methodology, reference parameters and assumptions used in their modelling, and also provided policy recommendations to encourage deployment of MCFCs in the oil sands.
CESAR, established in 2013, is an initiative to encourage and communicate research and critical analysis around the choices involved in transforming Canada’s energy systems. CESAR builds data resources and visualization tools, analyzes past energy systems and models energy futures, to inform policy and investment decisions on transforming Canada’s energy systems toward sustainability.
Backgrounder
Tackling Alberta’s greenhouse gas challenge
Alberta’s oil sands – 166 billion barrels recoverable with current technology as of 2014 – are the third-largest oil reserves in the world. Approximately 80 per cent of these reserves consist of “in situ” bitumen buried too deep to be mined from the surface.
Steam assisted gravity drainage, or SAGD, recovers bitumen by injecting steam into the reservoir. The heated bitumen flows by gravity into a well and is pumped to the surface.
The oil sands industry is subject to the Alberta government’s new carbon tax policy, with a $20-per-tonne CO2e tax to be implemented in 2017, to be increased to $30 per tonne CO2e in 2018. The policy includes a total emissions cap of 100 Mt CO2e per year over the entire industry.
The government also plans to phase out Alberta’s coal-fired power plants by 2030. These operations carry a high GHG-emissions intensity of 1,020 kilograms of CO2e per megawatt-hour of electricity produced, contributing to a carbon-intensive provincial electrical grid.
In SAGD operations, combustion of natural gas to produce steam accounts for 74 to 83 per cent of carbon dioxide emissions. Molten carbonate fuel cell (MCFC) technology offers the potential to capture 90 per cent or more of these emissions, either for use in enhanced oil recovery or for secure permanent storage underground. (For more on how MCFCs could capture CO2 while generating electricity, see this article in MIT Technology Review).
For widespread deployment of MCFCs at SAGD operations, however, Alberta would need to build a major “trunk” pipeline to transport compressed CO2 from the oil sands region to oil-producing areas for use in enhanced oil recovery or storage in saline aquifers. Also, more electrical grid transmission infrastructure would be required, to distribute the surplus clean electricity produced by MCFCs in the oil sands to locations that need the power.
Demonstration plant project underway
Cenovus Energy Inc., with Devon Canada and Shell Canada – all members of Canada’s Oil Sands Innovation Alliance (COSIA), is leading a joint industry project on a preliminary front-end engineering design for a 200-kilowatt pilot plant, COSIA says on its website. The proposal is to use MCFCs to capture CO2 from the 14-MW combined heat-and-power plant on the University of Calgary’s main campus, while generating low GHG-intensive electricity. The project, which will include a cost estimate for equipment installation and operation, is jointly funded by the three COSIA members and Alberta Innovates-Energy Environment Solutions.
Figure 5. A 1.4-megawatt installation of a molten carbonate fuel cell at a university in the United States. This is approximately the size of the facility that has been proposed for pilot testing at a location in Alberta. Image from FuelCell Energy, Inc. (http://www.fuelcellenergy.com)
“Combining MCFC technology with carbon capture is transformative because it could bring the cost of carbon capture down, making it a more viable solution – economically and environmentally,” says Wayne Hillier, director of COSIA’s greenhouse gases environmental priority area.
The University of Calgary has provided Cenovus with a letter of expression of interest to host the pilot plant, COSIA says. If the project goes ahead, it would remove about eight per cent of the carbon dioxide from the cogeneration plant’s emissions, or 10 tonnes of CO2 per day.
“The University of Calgary is a world leader in high-temperature fuel cell research, so it is a natural fit for us to be working with industry on this project,” says Viola Birss. “We see a lot of collaboration potential on this project, as well as opportunities for students to get hands-on experience with the technology.”
The student team that did the CESAR-coordinated study used data from COSIA, research papers, consultant studies and other sources to build their model and scenario projections.
Successful deployment of MCFCs “clearly depends on an infrastructure and policy which promotes the industrial and political integration of the oil sands with the electricity generation industries in Alberta,” says the team’s report.
Team advisor Song P. Sit says the students did a “very good” job on their project, although they tended to be more optimistic, and not as critical as he is, about MCFC technology’s potential. “This is perhaps understandable,” he said, since he has extensive experience with the considerable challenges in trying to commercialize new technologies.
Advisor Birss also thought the students “did a really good job . . . it was a well-done project.”
Sit says it’s unlikely the prevailing carbon price in Alberta, including the $30-per-tonne carbon tax to start in 2018, would pay for widespread MCFC deployment at SAGD facilities. Adding 500 to 1,000 MW of MCFCs would require CO2 prices in the range of $50 to $75 per tonne, he says. “I think it’s going to take a while.”
Figure 6. A 59-megawatt fuel cell park (the world’s largest) in South Korea. Image from FuelCell Energy, Inc. (http://www.fuelcellenergy.com)
Government would need to provide greater incentives not only to kick start a one- to five-megawatt demonstration plant, but to build a commercial-scale plant, Sit said. For example, he notes that the Alberta and federal governments together provided $1 billion toward Shell Canada’s Quest project to show the viability of a commercial carbon capture and storage plant capturing 1 million tonnes annually of CO2.
Another challenge, Sit said, is lack of technology competition. There is only one manufacturer, FuelCell Energy Inc. based in Danbury, Connecticut, which supplies commercial MCFC hardware, so there’s little incentive for the company to bring down its costs. On the other hand, less expensive CO2-capture technologies may emerge to compete against FuelCell Energy’s MCFC technology, which may incent the company to reduce capital costs.
Other risks of deploying MCFCs, Sit added, include that construction costs in the oil sands are still high, even with the current economic downturn.
Weighing benefits and risks
A July 2015 report by Jacobs Consultancy found that integrating MCFC with carbon dioxide capture into a SAGD facility would cut CO2 emissions by 88 per cent, from 2,194 tonners per day to 271 t/d – not including carbon credits for exporting 51 megawatts of clean power to the electricity grid. The report was prepared for Alberta Innovates-Energy and Environment Solutions and oil sands producers Cenovus Energy, BP, MEG Energy, Shell Canada and Suncor Energy.
Integrating an 80-MW MCFC into a SAGD facility producing 33,000 barrels per day would increase capital costs by more than 50 per cent or by about $450 million, to $1.29 billion for the MCFC-SAGD facility compared with $832 million for just the SAGD facility, according to the report. About 99 per cent of the additional costs result “from the fuel cells and carbon capture and compression equipment.”
However, the MCFC would lower the integrated facility’s operating costs by six per cent (assuming that surplus power can be sold to the grid), reduce make-up water requirements for generating steam, and eliminate the need to purchase power for the SAGD operation.
Integrating the MCFC into the SAGD facility would be economically limited to fuel and water, “and therefore presents very little technical risk. In addition, the MCFC itself is commercialized,” said the report.
It cautioned, however, that although most components of MCFC with carbon dioxide capture are commercial or near-commercial, “the reliable operation and maintenance costs resulting from an installation of this size in northern Alberta are (potential) risks.” There are likely to be unforeseen challenges associated with integrating the operation and maintenance of MCFC with SAGD oil production, said the report.
The consultancy’s recommendations included a design study to determine location, feasibility and estimated capital cost of an MCFC-SAGD demonstration facility in Alberta, “to confirm reliability, operability, and commercial readiness, and to highlight other development issues.”
In a separate study published last year in the International Journal of Greenhouse Gas Control, Richard Hill from Jacobs Consultancy and several co-authors reported that MCFC technology “has the potential to significantly reduce the carbon capture cost at a SAGD facility and to export low GHG intensity electric power.”
If enough surplus clean power is produced with the fuel cells, it could actually in the long term reduce carbon emissions from bitumen production to below zero, the authors said. “If reliably produced, excess power generation may provide CO2 credits by offsetting Alberta grid electricity, possibly leading to a negative carbon footprint in bitumen production.”
Footnotes
1 Jacobs Consultancy 2015. Evaluation of Integrating a Molten Carbonate Fuel Cell (MCFC) with a SAGD Facility. Alberta Innovates- Energy and Environment Solutions (http://www.ai-ees.ca/media/15155/2251_mcfc_integration_evaluation_-_final_report_-_2015-07-30.pdf)
2 Hill et al. 2015. Application of molten carbonate fuel cell for CO2 capture in thermal in situ oil sands facilities. International Journal of Greenhouse Gas Control 41: 276-284. (http://www.sciencedirect.com/science/article/pii/S1750583615300323?np=y)